، قزوین , (اخبار رسمی): امروزه از دیگهای بخار در صنایع غذایی، سیستمهای گرمایشی و نیروگاهها استفاده میشود و آنچه مشخص است این است که استفاده از دیگهای بخار از اوایل قرن هجدهم میلادی با پیدایش ماشینهای بخار در صنعت رایج شده است.
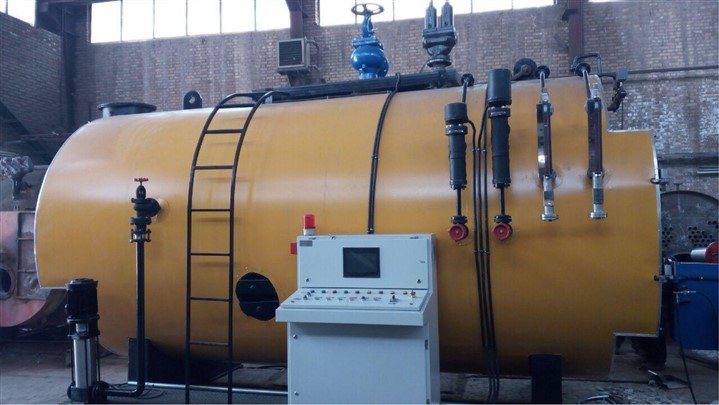
دیگ های بخار اولیه از ظرف سر بستهای از ورقهای آهنی که بر روی هم برگردانده شده و پرچ شده بودند در اشکال کروی ساده تا انواعی پیچیدهتر نظیر دیگهای واگن وات که شبیه والگن سر پوشیدهای بود ساخته میشدند.
این ظروف بر روی دیوارهای از آجر بر روی آتش قرار داشتند و برای رساندن حرارت به نقاطی از ظرف که مقابل آتش نبودن از کانالهای آجری استفاده میشد این دیگها را بیرون سوز مینامند و بزرگترین اشکال آنها ایجاد رسوب و لجن در پایینترین نقطه یعنی بالای سطح داغ آتش بود که سبب جلوگیری تماس فلز و آب میشد که نتیجه آن بالا رفتن درجه حرارت فلز (حدود 500 درجه سلسیوس) و تغییر شکل و در نهایت سوختن آن بود و هر چند فشار کاری دیگهای بخار آن زمان در حدود فشار اتمسفر بود ولیکن این مشکل با عث خراب شدن و یا مواردی ترکیدن دیگ بخار میشد.
با افزایش تقاضا برای تولید دیگهای با فشار بالاتر، ساخت دیگهایی که درون سوز بودند آغاز شد که از استوانههای فلزی ساخته میشدند و کوره نیز به شکل استوانه در درون مخزن استوانهای قرار میگرفت و محصولات احتراق که در آن زمان بیشتر به صورت جامد (زغال سنگ) بودند از روی صفحهای مشبک به درون کوره انتقال مییافتند و درون کوره میسوختند.
در این دیگهای بخار اولیه برای بهره برداری از دمای گازهای خروجی دودکش، از طریق انتقال آنها از کوره به کانالهای تعبیه شده در زیر مخزن استوانهای و در نهایت هدایت به سمت دودکش خروجی دیگ بخار اقدام به بالا بردن راندمان میکردند ولیکن با توجه به اینکه فلز مخزن زیر کوره که به دلیل جمع شدن گل ولای حاصل از آب و کاهش تماس آن با آب مخزن دیگ بخار دارای دمای بیشتری میشد ، همان مشکل تغییر خاصیت فلز تاحدودی وجود داشت هرچند دمای گازهای کانال خیلی کمتر از قبل بود.
در ادامه فرآیند پیشرفت تولید دیگهای بخار صنعتی، دیگهای معروف به لوله آتشی عقب خشک (FireTube & DryBack) طراحی و ساخته شدند که در این دیگها با قراردادن لولههای متعدد داخل مخزن دیگ بخار، گازهای داغ انتهای کوره را از داخل آنها عبور داده و در نهایت از قسمت دودکش دیگ بخار خارج میشدند ولی از مشکلات این دیگها وجود سطح عایقکاری شده در انتهای کوره بود که علاوه بر اتلاف انرژی حرارتی، حین کار و یا انتقال در اثر لرزش و ضربههای ایجاد شده در کوره باعث صدمه دیدن عایق کاری و در نتیجه سوختن فلز انتهای کوره میشود که این مشکل در نسل بعدی دیگهای بخار صنعتی با قرار دادن انتهای کوره در داخل آب تا حدود زیادی مرتفع شد و سطح حرارتی دیگ افزایش یافت در این طرح که به نام طرح لوله آتشی و عقبتر (FierTube & WetBack) معروف است به طور معمول بسته به ظرفیت دیگ بخار از لحاظ انرژی حرارتی ورودی، به دو صورت دوپاس و سه پاس ، طراحی و ساخته میشوند.
راندمان حرارتی در دیگهای جدید با اعمال سطح حرارتی قابل قبول و عایق کاری مناسب به حدود 85% قابل دستیابی است. گامی هرچند کوتاه به دنبال دیگ بخار کورنیش تک کورهای برداشته شد و و آن دیگ بخار بزرگتر دو کورهای لانکاشیر بود که تحت امتیاز FAIRBAIRN و HETHERINGTON در سال 1844 به ثبت رسید که تا اوایل دهه 1950 میدان دار دیگهای صنعتی بود. احتمالا بیش از هزار عدد از این دیگ بخار هنوز در انگلستان کار میکنند، گرچه امروزه آنها را با نوع پرصرفهتر و چند لولهای به نام «ECONOMICS» جایگزین میکنند.
باید در نظر داشت که هر چه سطوح در معرض حرارت دیگ بخار زیادتر باشد مقدار حرارت جذب شده از مصرف مقدار معینی سوخت، یعنی بازده بازیافت حرارتی، بیشتر خواهد بود.
برای این منظور تعداد بیشماری لولههای باریک که از آنها گازهای گرم جریان دارد و در داخل آب قرار دارند عامل ازدیاد سطوح گرم هستند و در عین حال نیازی به کانال گازهای گرم در پایین دیگ بخار و دو طرف آن نخواهد بود. این نوع دیگها یکپارچه هستند.
هر چه لولهها بلندتر و باریکتر باشند، سطوح انتقال حرارت کارایی بیشتری خواهند داشت. این دیگهای چند لولهای برای ظرفیت معینی، کم حجمتر از نمونههای پیشین خود هستند و نیازی به آجرکاری ندارند. این دیگها در کشتیها و لکوموتیوها که فضا نقش تعیین کننده دارد، کاربرد زیادی دارند.
تعدادی از دیگهای اولیه کشتیها جهت استفاده بیشتر از فضا، دارای سطح مقطع چهار گوش بودند که بر اثر پارگی گوشهها، منجر به انفجارات شدید این دیگها میشود.
### پایان خبر رسمی