، تهران , (اخبار رسمی): تولید اسید سولفوریک از زمان کشف آن توسط جابر ابن حیان تاکنون با چه تغییراتی همراه بوده و در حال حاضر تولید صنعتی این ماده چگونه صورت میگیرد؟ آیا با موارد کاربرد این اسید آشنا هستید؟ در این مقاله سولفوریک اسید را از ابتدای کشف آن تا به امروز بررسی خواهد شد.
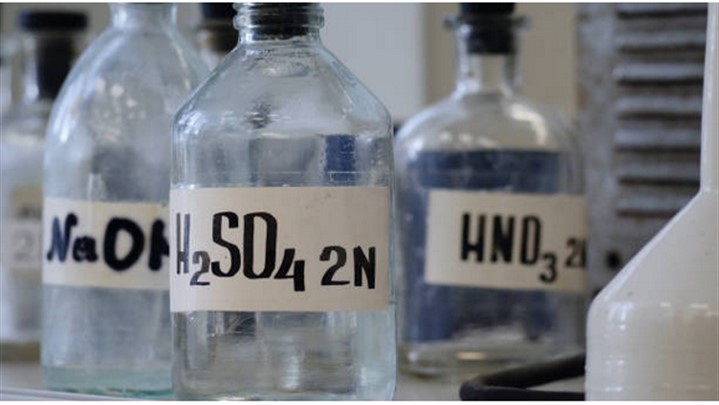
اسید سولفوریک (سولفات هیدروژن، H2SO4) که در گذشته به آن جوهر گوگرد نیز گفته میشد، اسید معدنی بسیار قوی است که به هر نسبتی در آب حل میشود و دارای 0/5=pH است.
این اسید دارای مولکولهای قطبی بوده که میتوانند با یکدیگر پیوند هیدروژنی برقرار کنند، لذا اسید سولفوریک مایعی با نقطه جوش بالا و ویسکوز (گرانروی زیاد) به شمار میرود.
اسید سولفوریک میل ترکیبی زیادی با آب دارد و در اثر واکنش با آن گرمای شدیدی آزاد میکند. افزودن آب به اسید سولفوریک غلیظ بسیار خطرناک است، زیرا در اثر حرارت حاصل از واکنش اسید و آب، آب گرم ممکن است به اطراف پراکنده شود، زیرا آب به دلیل دانسیته پایینتر تمایل دارد روی اسید قرار گیرد.
اولین بار جابر حیان در مورد تقطیر شوره یا زاج سبز که منجر به تولید اسید سولفوریک میشود، سخن میگوید. اما در بسیاری از متون، کشف اسید سولفوریک را به زکریای رازی نسبت دادهاند. وی با تقطیر خشک کانیهایی که شامل سولفات آهن (II) (زاج سبز) و سولفات مس (II) (کات کبود) توانست اسید سولفوریک به دست آورد. در اثر حرارت دادن هر یک از این نمکها اکسید آهن (II) و اکسید مس (II) به همراه آب و گوگرد تری اکسید حاصل میشود، که به واسطه ترکیب آب و گوگرد تری اکسید، محلول رقیق اسید سولفوریک ایجاد میشود.
در قرن هجدهم، جان گلوبر، اسید سولفوریک را از سوزاندن گوگرد و نیترات پتاسیم در مجاورت بخار آب تهیه کرد. در سالهای بعد، جان روبک اسید سولفوریک را با غلظت 40-35% در ظروف سربی تولید میکرد.
در سال ۱۸۲۷ با معرفی برجهای سربی برای بازیافت اکسیدهای نیتروژن توسط گیلوساک قدم مهمی در تولید اسید سولفوریک برداشته شد و نخستین بهینهسازی انجام یافته بر روی آن مبتنی بر افزودن هوای محیط به سیستم به منظور پیشرفت بیشتر واکنش بود. همچنین به جای استفاده از سیستم ناپیوسته (batch) از سیستم پیوسته سوزاندن گوگرد در آن استفاده شد.
32 سال بعد جان گلاور، اولین برج حذف نیتروژن و افزایش غلظت اسید سولفوریک را معرفی کرد. برجهای گیلوساک و گلاور اولین برج حذف نیتروژن و افزایش غلظت اسیدسولفوریک را معرفی کرد. برجهای گیلوساک و گلاور بخشهای اصلی سیستمی را که ما امروزه به نام فرآیند تولید اسید سولفوریک در اتاق سربی میشناسیم را تشکیل میدهند.
کارهای ابتدایی روی فرآیند مجاورت (تماسی) توسط فیلیپس در سال 1831 انجام گرفت. در آن زمان تحقیقات روی انجام واکنش بین گوگرد دی اکسید و اکسیژن با نسبتهای استوکیومتری متمرکز بود. در سال ۱۹۰۱ با گشوده شدن رموز پارامترهای فرآیندی واکنش اکسیداسیون کاتالیکی گوگرد دی اکسید توسط شرکت BASF فرآیند مدرن مجاورت (تماسی) متولد شد و اولین کارخانه تولید اسید سولفوریک به روش مجاورت (تماسی) توسط آن شرکت و در آمریکا ساخته شد.
تولید اسید سولفوریک
اسید سولفوریک، یکی از مهمترین مواد شیمیایی در صنعت است که با استفاده از فرآیند مجاورت (تماسی) تولید میشود. به طور کلی فرآیند تولید اسید سولفوریک چهار مرحله دارد:
1- استخراج گوگرد
2- تبدیل گوگرد به گوگرد دی اکسید
3- تبدیل گوگرد دی اکسید به گوگرد تری اکسید
4- تبدیل گوگرد تری اکسید به اسید سولفوریک
یکی از مهمترین منابع تهیه گوگرد، نفت و گاز طبیعی است. ترکیبات حاوی گوگرد هم به شکل ترکیبات آلی و هم ترکیبات معدنی (مانند هیدروژن سولفید)، هر دو باید از نفت یا گاز طبیعی که به عنوان سوخت یا مواد خام شیمیایی به کار می روند، زدوده شوند.
یکی دیگر از منابع گوگرد به شکل گوگرد دی اکسید حاصل تصفیه فلزات است. بسیاری از سنگ معادن فلزات به شکل ترکیبات سولفیدی بوده که پس از حرارت دادن آنها اکسید فلزات و گوگرد دیاکسید تولید میشود. به عنوان مثال در تولید سرب، 2PbS + 3O2 ——–> 2PbO + 2SO2
فلزاتی مانند مس، روی، آهن، مولیبدیم و نیکل را نیز از سنگ معدن سولفیدی آنها استحصال میکنند.
از منابع دیگر تولید گوگرد دی اکسید میتوان به احتراق گاز H2S و یا بازیافت اسید سولفوریک مصرف شده اشاره کرد. در روش صنعتی تولید اسید سولفوریک، ابتدا گوگرد با خلوص بالا را با گرم کردن غیر مستقیم، به وسیله کویل بخار، به حالت مایع در میآورند. گوگرد در دمای ۱۵۰ درجه سانتی گراد به حالت مایع در میآید. و به راحتی میتوان آن را به کمک پمپ مخصوص، جهت سوزاندن به درون کوره احتراق انتقال داد.
مقدار جرم گوگرد مذاب منتقل شده به درون کوره احتراق باید تنظیم شود. این عمل به دو روش زیر انجام میشود:
1- کنترل مسیر برگشتی به درون حوضچه
2- تنظیم سوزن مشعل کوره
با توجه به گنجایش هر کوره، به ازای هر تن اسید ۹۸ درصد، ۲۰۰ کیلوگرم گوگرد وارد کوره میشود. گوگرد در کوره احتراق در دمای ۱۰۰۰-۹۵۰ درجه سانتی گراد به گوگرد دیاکسید تبدیل میشود. گرما + S + O2 ———> SO2
اکسیژن نیز از طریق هوای فشرده توسط دمنده هوا تامین میشود و پیش از ورود به کوره، برای جلوگیری از پایین آمدن دمای کوره، توسط مبدل گرمایی تا دمای ۱۵۰ درجه سانتیگراد گرم میشود. پنتا اکسید وانادیم به عنوان کاتالیزور تبدیل SO2 به SO3 در برج مخصوص که به صورت چهار لایه قرار گرفته، استفاده میشود. هر دو لایه، متصل به هم بوده و تنها با یک صفحه فلزی مشبک از یکدیگر جدا شدهاند. مقدار کاتالیزور در این چهار لایه متفاوت بوده، به طوری که لایه چهارم که پایینترین لایه است شامل ۷۰ درصد کاتالیزگر و بقیه لایهها به ترتیب حاوی ۲۰، ۷ و ۳ درصد کاتالیز هستند.
مقدار کل کاتالیزور به ازای هر تن اسید ۹۸ درصد ۲۰۰ کیلوگرم است. گاز SO2 تولید شده دمای بالایی دارد و اگر با این دما وارد برج حاوی کاتالیزور شود موجب تخریب کاتالیزور میشود. لذا پیش از ورود به برج دمای آن می بایست کاهش یابد. برای این منظور پیش از ورود این گاز به برج نخست آن را وارد دیگ تولید بخار میکنند. تا گرمای خود را به آب درون دیگ منتقل کرده، تا دمای ۵۰۰ درجه سانتی گراد خنک شود.
در این مرحله احتمال وجود ذرههای گرد و غبار و سیلیس و عنصرهایی مانند سرب و آرسنیک (ناخالصیهای احتمالی گوگرد) در گاز حاصل از احتراق وجود دارد، بنابراین برای جلوگیری از ورود آنها به برج حاوی کاتالیزور، باید گاز را از صافی سیلیسی ویژه گذراند. در این صافی افزون بر به دام انداختن ناخالصیها، با تزریق هوای خشک و خنک به گاز، کمبود اکسیژن نیز برطرف شده ، دما به ۴۵۰ درجه سانتی گراد میرسد که دمایی مناسب برای ورود به برج کاتالیزور است. واکنش تبدیل SO2 به SO3 در برج گرماده است.
همانطور که گفته شد گرمای زیاد به کاتالیزور آسیب می رساند، لذا برای جلوگیری از این مشکل گاز SO3 وارد مبدل گرمایی میشود و تا دمای ۴۵۰ درجه سانتی گراد خنک میشود. گاز SO3 تولید شده به منظور از دست دادن مقدار ناچیز SO2 همراه خود می بایست از لایه های سوم و چهارم کاتالیزور نیز بگذرد تا باقیمانده SO2 نیز به SO3 تبدیل شود. گاز SO3 خارج شده از لایه چهارم وارد مبدل گرمایی دیگری شده و تا ۲۴۰ درجه سانتی گراد خنک میشود. آنگاه وارد برج اولئوم و سرانجام وارد برج اسید میشود.
در برجهای نهایی گاز SO3 و اسید سولفوریک، در خلاف جهت یکدیگر حرکت میکنند. به این ترتیب که اسید سولفوریک به صورت پاششی از بالای برج به پایین حرکت میکند و گاز از پایین برج روانه بالای برج میشود. طی این حرکت گاز SO3 جذب اسید شده و اولئوم (اسید سولفوریک دودکننده یا پیروسولفوریک اسید) را ایجاد میکند که همان اسید سولفوریک با درصد بالایی از SO3 است.
کاربرد اسید سولفوریک
کودهای شیمیایی
1- اسید فسفریک
اسید فسفریک خود ماده اولیه تولید کودهای فسفاته است. بخش عمدهای از اسید سولفوریک تولید شده صرف تولید اسید فسفریک به روش مرطوب (wet process) میشود.
2- کود آمونیوم سولفات
در تولید کود آمونیوم سولفات که یکی از کودهای پرمصرف کشاورزی است، از اسید سولفوریک و آمونیاک استفاده میشود.
3- کود سوپر فسفات (سوپر فسفات نرمال، NSP)
این کود فسفاته بر اثر واکنش بین اسید سولفوریک و سنگ فسفات تولید میشود. در این فرآیند فسفات موجود در سنگ فسفات، به مونو کلسیم فسفات مونوهیدرات تبدیل میشود. این نوع کود شیمیایی کمترین مقدار از P2O5 را در بین تمام کودهای شیمیایی فسفاته دارا است که باعث محدود شدن مصرف آن میشود.
4- استفاده از خود اسید سولفوریک، مقدار کمی از اسید سولفوریک در کودهای شیمیایی به صورت مستقیم در مخلوط کودهای مایع مورد استفاده قرار میگیرد.
صنایع معدنی و فلزی
از اسید سولفوریک در استخراج بسیاری از فلزات استفاده میشود.
1- استخراج فلزاتی چون مس، روی و سرب
در استخراج و تغلیظ سنگ معدن فلزات مس، روی و سرب از اسید سولفوریک استفاده میشود.
2- استخراج اورانیوم و وانادیوم
در اوایل دهه 1980 مقدار بسیار زیادی از اسید سولفوریک جهت استخراج اورانیوم و به دنبال آن محصول جانبی آن که وانادیم بود، شد. اما به دنبال محدودیت های ایجاد شده توسط سازمان ملل متحد به منظور استخراج اورانیوم، مصرف اسید سولفوریک در این حوزه با کاهش زیادی روبرو شد.
3- صنایع آهن و فولاد
از اسید سولفوریک در صنایع فولاد به منظور بازیافت گازهای آمونیاک که منجر به تولید نمک آمونیوم سولفات (محصول جانبی در صنایع فولاد) میشود و همچنین برای رسوبزدایی در عملیات اکسیدهای فلزی، چربیها، نمکها و حتی زنگزدایی از سطح فولاد، استفاده میشود.
4- تولید نمک سولفات
از اسید سولفوریک در تولید نمکهای سولفات مس (کات کبود)، منگنز، نیکل، آهن (زاج سبز و زاج سفید)، سدیم، آلومینیوم و روی استفاده میشود.
علاقهمندان جهت کسب اطلاعات بیشتر در خصوص مواد شیمیایی میتوانند به مرجع مواد شیمیایی ایران مراجعه کنند.
### پایان خبر رسمی