، تهران , (اخبار رسمی): 13 مشکلات قالب گیری تزریق پلاستیک و راه حل
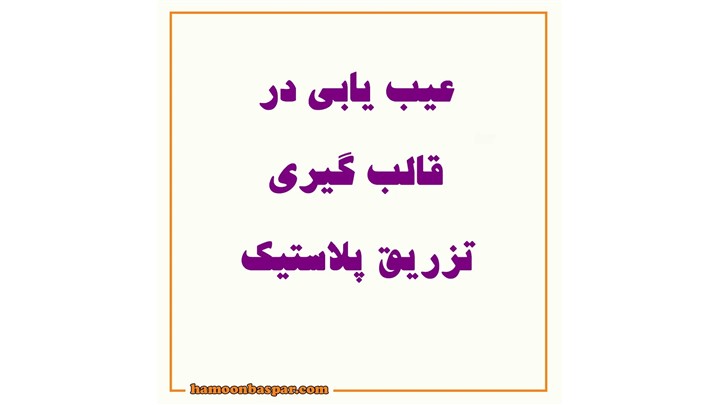
از مزایای قالبگیری تزریق پلاستیک برای روشهای ساخت قطعات میتوان به سرعت تولید سریع، راندمان بالا، اتوماسیون عملیات، شکلها و انعطافپذیری اندازه اشاره کرد. علاوه بر این، محصولات قالبگیری تزریقی از نظر اندازه دقیق هستند، به راحتی قابل تعویض هستند و قطعات قالب را میتوان به اشکال پیچیده تبدیل کرد. این روش سازگار با محیط زیست برای زمینه های پردازش قالب گیری مانند تولید انبوه و محصولات شکل پیچیده مناسب است.
با این حال، اگرچه اپراتورها با ماشینهای خاص و مهارتهای عملیاتی در فرآیند قالبگیری قطعات پلاستیکی آشنا هستند، نقصهای مختلف قالبگیری سریع در طراحی قالب و مواد اجتنابناپذیر است. هدف این مقاله حل مشکلات و راه حل های قالب گیری تزریق پلاستیک است که عمدتاً به شرح زیر است. البته این مساله را هم در نظر داشته باشید که استفاده از مستربچ افزودنی بسیاری از مشکلات محصولات پلاستیکی را مرتفع کرده است.
علل این مشکلات ناشی از مواد خام، قطعات پلاستیکی یا طراحی قالب، فرآیندهای قالب گیری و غیره را تجزیه و تحلیل کنید و راه حل های مرتبط را پیشنهاد دهید.
1. شات های کوتاه
شات های کوتاه پدیده ای است که در آن حفره قالب را نمی توان به طور کامل پر کرد.
علل:
(1) دمای قالب، دمای مواد یا فشار و سرعت تزریق بسیار پایین است
(2) پلاستیک سازی ناهموار مواد خام
(3) اگزوز ضعیف
(4) نقدینگی ناکافی مواد خام
(5) قطعه خیلی نازک است یا اندازه دروازه خیلی کوچک است (6) مذاب پلیمری به دلیل طراحی ساختاری غیرمنطقی زودرس شده است
راه حل ها:
مواد: از مواد سیال بیشتری استفاده کنید
طراحی قالب:
(1) دیوار ضخیم را قبل از پر کردن دیوار نازک پر کنید تا از پدیده احتباس جلوگیری کنید.
(2) تعداد گیت ها و اندازه دونده را به طور مناسب افزایش دهید تا نسبت فرآیند و مقاومت جریان کاهش یابد.
(3) موقعیت و اندازه درگاه اگزوز باید به درستی تنظیم شود تا از پدیده اگزوز ضعیف جلوگیری شود.
دستگاه:
(1) بررسی کنید که آیا شیر چک و دیواره داخلی سیلندر مواد به طور جدی فرسوده شده اند یا خیر
(2) بررسی کنید که آیا درگاه تغذیه دارای مواد است یا اینکه پل شده است.
روند:
(1) فشار تزریق و سرعت تزریق را برای افزایش حرارت برشی افزایش دهید
(2) مقدار تزریق را افزایش دهید
(3) دمای سیلندر مواد و دمای قالب را افزایش دهید
2. تله های هوایی در تزریق پلاستیک
تله هوا جایی است که هوا در حفره محبوس می شود تا حباب هایی در قطعه ایجاد شود.
علل: به دلیل عدم امکان خروج هوا از سطح جداکننده، قوچ یا دریچه هنگام برخورد دو جبهه مذاب ایجاد می شود.
راه حل: طراحی سازه: ناهماهنگی ضخامت را کاهش دهید و سعی کنید از ضخامت یکنواخت دیوار اطمینان حاصل کنید.
طراحی قالب:
(1) یک دریچه در آخرین مکان پر شده اضافه کنید
(2) طراحی مجدد دروازه و سیستم دونده
روند:
(1) سرعت تزریق آخرین مرحله را کاهش دهید
(2) دمای قالب را افزایش دهید
پیشنهاد مطالعه: مستربچ سفید چیست و چه کاربردی دارد
3. رفع مشکل شکنندگی محصولات پلاستیکی
شکنندگی این است که قسمت پلاستیکی به راحتی در جایی ترک خورده یا شکسته می شود
علل:
(1) شرایط خشک مناسب نیست. استفاده از مواد بازیافتی بیش از حد
(2) تنظیم دمای تزریق اشتباه است
(3) تنظیمات سیستم گیت و رانر مناسب نیستند
(4) قدرت علامت ذوب بالا نیست
راه حل ها:
مواد:
(1) شرایط خشک کردن مناسب را قبل از قالب گیری تزریقی تنظیم کنید
(2) کاهش استفاده از مواد بازیافتی و افزایش نسبت مواد خام
(3) از پلاستیک با استحکام بالا استفاده کنید. طراحی قالب: اندازه رانر اصلی، رانر شاخه و دروازه را افزایش دهید
ماشین: یک پیچ با طراحی خوب انتخاب کنید تا توزیع دما در حین پلاستیک سازی یکنواخت تر شود
روند:
(1) دمای سیلندر و نازل مواد را کاهش دهید
(2) فشار برگشتی، سرعت پیچ و سرعت تزریق را کاهش دهید
(3) دمای مواد و فشار تزریق را افزایش دهید، قدرت ذوب را بهبود بخشید
4. رفع مشکل علائم سوختگی در تزریق پلاستیک
علائم سوختگی این است که گاز موجود در حفره را نمی توان به موقع خارج کرد و در نتیجه در انتهای جریان سیاه می شود.
علل:
(1) هوای داخل حفره را نمی توان به موقع خارج کرد.
(2) تخریب مواد: دمای مذاب بیش از حد. سرعت پیچ ابری؛ طراحی نامناسب سیستم دونده
راه حل ها:
طراحی قالب:
(1) یک سیستم اگزوز را به مکانی که گاز خروجی به راحتی تولید می شود اضافه کنید
(2) اندازه سیستم دونده را افزایش دهید
روند:
(1) فشار و سرعت تزریق را کاهش دهید
(2) دمای بشکه را کاهش دهید
(3) بررسی کنید که بخاری و ترموکوپل به درستی کار می کنند.
5. مشکل فلش در تزریق پلاستیک
به این معنی که پلاستیک اضافی روی قسمت جدا کننده قالب یا اجکتور وجود دارد.
علل:
(1) نیروی گیره ناکافی
(2) قالب دارای نقص است
(3) شرایط قالب گیری نامعقول است
(4) طراحی نامناسب سیستم اگزوز
راه حل ها:
طراحی قالب:
(1) قالب را معقولانه طراحی کنید تا اطمینان حاصل شود که وقتی قالب بسته می شود، قالب بسته می شود
(2) اندازه درگاه اگزوز را بررسی کنید
(3) تمیز کردن سطح قالب
ماشین: دستگاه را با فرآیند اندازه مناسب تنظیم کنید:
(1) زمان تزریق را افزایش دهید و سرعت تزریق را کاهش دهید
(2) دمای بشکه و دمای نازل را کاهش دهید
(3) فشار و فشار تزریق را کاهش دهید
پیشنهاد مطالعه:
6. لایه لایه شدن محصولات در تزریق پلاستیک
به سطح قسمتی گفته می شود که می توان لایه به لایه جدا کرد.
علل:
(1) مخلوط کردن سایر پلیمرهای ناسازگار
(2) عامل آزادسازی بیش از حد مورد استفاده در طول قالب گیری
(3) دمای رزین ناسازگار است
(4) رطوبت بیش از حد
(5) دروازه و مسیر جریان دارای زوایای تیز هستند
راه حل ها:
مواد: از ناخالصی های ناسازگار یا مواد بازیافتی آلوده مخلوط شده با مواد خام خودداری کنید
طراحی قالب: همه رانرها یا دروازه ها را با زوایای تیز پخ کنید
روند:
(1) دمای بشکه و قالب را افزایش دهید
(2) خشک کردن مناسب مواد قبل از قالب گیری
(3) از استفاده بیش از حد عامل آزاد کننده خودداری کنید
7. جت کردن در تزریق پلاستیک
اثر اسپری ناشی از جریان بیش از حد مذاب است که معمولاً مارپیچ است.
علل:
(1) اندازه دروازه خیلی کوچک است و با سطح مقطع بزرگ رو به سطح محصول است.
(2) سرعت پر کردن خیلی سریع است
راه حل ها:
طراحی قالب:
(1) اندازه دروازه را افزایش دهید
(2) دروازه جانبی را به دروازه لبه تغییر دهید
(3) پین توقف جلوی دروازه را افزایش دهید
8. خطوط جریان در تزریق پلاستیک
خطوط جریان، عیوب قالبگیری هستند که روی سطح محصول موجدار هستند که به عنوان نوعی پرش قورباغهای ناشی از جریان آهسته مذاب شناخته میشوند.
علل:
(1) دمای قالب و دمای مواد خیلی کم است
(2) سرعت تزریق و فشار بسیار آهسته است
(3) اندازه کانال جریان و دروازه بسیار کوچک است
(4) با توجه به ساختار محصول، هنگامی که جریان پر شدن ایجاد می شود، شتاب بسیار زیاد است.
راه حل: طراحی قالب:
(1) اندازه چاه سرد را در کانال جریان افزایش دهید
(2) اندازه دونده ها و دروازه ها را افزایش دهید
(3) اندازه کانال اصلی را کوتاه کنید یا به رانر داغ تغییر دهید
روند:
(1) سرعت تزریق را افزایش دهید
(2) فشار و فشار تزریق را افزایش دهید
(3) زمان نگهداری فشار را افزایش دهید
(4) دمای قالب و دمای مواد را افزایش دهید
9. مه
یک تغییر رنگ ابر مانند در نزدیکی دروازه رخ می دهد. دلیل آن شکستگی مذاب است.
علل: اگر دروازه خیلی کوچک باشد یا حفره چسب خیلی نازک باشد، سرعت جریان مذاب زیاد است، سطح شکسته کوچک است، سرعت برش زیاد است و تنش برشی اغلب افزایش مییابد به طوری که لاستیک مذاب می شکند و تغییر مه رخ می دهد.
راه حل: شبیه سازی Moldflow. پیش بینی دما، سرعت برشی و تنش برشی مذاب عبوری از ناحیه باریک فوق امکان پذیر است. جریان قالب معمولاً حد بالایی برای دما، سرعت برشی و تنش برشی مواد پلاستیکی مختلف ارائه میکند. مهندسان Moldflow میتوانند تنظیماتی را بر اساس نتایج تحلیل انجام دهند تا اندازه دروازه و ضخامت دیواره حفره مناسب را در ورودی چسب برای از بین بردن مه پیدا کنند.
10. رگه ها
رگه هایی هستند که در آنها آب، هوا یا زغال سنگ در جهت جریان در امتداد سطح قطعه توزیع می شود.
علل:
(1) میزان رطوبت در مواد خام بسیار زیاد است
(2) هوا در مواد خام به دام افتاده است
(3) تخریب پلیمر: مواد آلوده است، دمای بشکه بسیار بالا است. حجم تزریق ناکافی
راه حل ها:
طراحی قالب:
بررسی کنید که آیا موقعیت اگزوز کافی است یا خیر.
(1) ماشین قالب گیری تزریقی و قالب مناسب را انتخاب کنید
(2) هنگام تعویض مواد، مواد قدیمی را به طور کامل از بشکه تمیز کنید
(3) بهبود سیستم اگزوز
(4) دمای مذاب، فشار تزریق یا سرعت تزریق را کاهش دهید
11. علائم سینک
پدیده ای است که در آن سطح قطعه در ضخامت دیواره مقعر است.
علل:
(1) فشار تزریق یا فشار نگه داشتن خیلی کم است
(2) زمان نگهداری یا زمان خنک شدن خیلی کوتاه است
(3) دمای مذاب یا دمای قالب خیلی زیاد است
(4) طراحی نامناسب ساختار قطعات
راه حل ها:
طرح:
(1) سطح راه راه روی سطحی که در آن فرورفتگی به راحتی ایجاد می شود
(2) اندازه دیواره ضخیم قطعه کار را کاهش دهید، نسبت ابعاد را به حداقل برسانید و نسبت ضخامت دیوار مجاور باید در 1.5 ~ 2 کنترل شود و سعی کنید یک انتقال صاف انجام دهید. ضخامت دنده ها، سوراخ ها و دنده ها را دوباره طراحی کنید. ضخامت آنها به طور کلی به عنوان 40-80٪ ضخامت دیوار اصلی توصیه می شود.
روند:
(1) فشار و فشار تزریق را افزایش دهید
(2) اندازه دروازه را افزایش دهید یا موقعیت دروازه را تغییر دهید
12. خطوط جوش
خطوط جوش به عیب سطح ناشی از جوشکاری دو جریان به یکدیگر اشاره دارد.
علل: اگر سوراخ ها، درج ها یا روش های قالب گیری تزریقی چند دروازه ای در قطعات ساخته شده وجود داشته باشد یا ضخامت دیواره قطعات ناهموار باشد، ممکن است خطوط جوش ایجاد شود.
راه حل ها:
مواد: سیالیت مذاب پلاستیک را افزایش می دهد
طراحی قالب:
(1) موقعیت دروازه را تغییر دهید
(2) یک شکاف تهویه اضافه کنید
روند:
(1) دمای مذاب را افزایش دهید
(2) مقدار عامل رهاسازی را کاهش دهید
13. Warpage
مشکل ترین مشکل برای حل در طراحی و تولید قطعات پلاستیکی تاب است.
علل:
(1) ساختار قالب: ریختن، سیستم خنک کننده و سیستم تخلیه
(2) ساختار محصول: ضخامت دیوار قطعات پلاستیکی تغییر می کند، با هندسه منحنی یا نامتقارن، دنده ها و طراحی ستون BOSS معقول نیست
(3) فرآیند تولید: قطعات پلاستیکی به طور کامل خنک نشده اند و منحنی های نگهدارنده تزریق و فشار غیر منطقی هستند
(4) مواد پلاستیکی: مواد پلاستیکی بدون پرکننده اضافه شده و اندازه انقباض است.
راه حل ها:
(1) دمای قالب ناپایدار است. قالب متعادل سرمایش/گرمایش را ارائه دهید
(2) ضخامت بخش نامنظم شکل و اندازه محصول با توجه به ویژگی های رزین دوباره طراحی شده است
در WayKen، در برخی از موارد قالبگیری تزریقی نمونه اولیه، با مشکلات و راهحلهای مشابه زیادی در قالبگیری تزریق پلاستیک مواجه شدهایم. به منظور ایجاد محصولات قالبگیری تزریقی برای مشتریان خود، ما جزئیات قطعات ماشینهای قالبگیری تزریقی و قالبگیری تزریقی را گام به گام قبل از ساخت قطعات و در طول فرآیند قالبگیری تزریقی به شدت بررسی میکنیم.
### پایان خبر رسمی